Crops are constantly exposed to pests and other external agents such as fungi, animals or insects that deteriorate them and can cause large losses to farmers.
Besides, plants sometimes have nutrient deficiencies because of certain soil conditions or climate that need to be counteracted with an additional contribution.
With such a background, the need to use agrochemicals arises. These products have become essential to get better production, higher crop yields, more protection against external agents and diseases that deteriorate them and, ultimately, to ensure their good condition when it comes to marketing and consuming their fruits.
In short, agrochemicals are responsible for preventing a decrease of between 30% and 40% in plant production worldwide each year.
But these chemicals have peculiarities that make not any packaging suitable for them.
Agrochemicals require specific storage, transport and handling conditions within prepared packaging. All agrochemical warehouses must meet safety requirements. In addition, they should be kept away from contaminating water or land, and should be stored vertically with the closure facing up, even if they have already been opened. Besides, their labels must include information on phone numbers and procedures for acting in an emergency.
They must be transported in plastic containers specifically made for agrochemicals with secure closures and resistant enough. They should never be transported outside the original packaging, which is specifically prepared for such products. In addition, they will also have to be placed in the same storage position, vertically, with the closure facing up and always avoiding their exposure to rain or sun.
In the case of handling agrochemicals, it is important to have always the right equipment, make all mixtures in places away from any water source and ensure that the containers are always closed when not in use.
Taking into account all the requirements of these products both for their storage and for their transport and handling, it is worth highlighting the importance of plastic packaging for agrochemicals throughout the process.
These containers are prepared to house aggressive chemicals without deteriorating, withstand certain temperatures, pressure, etc., and ultimately allow them to be stored, transported and handled safely.
Characteristics of the agrochemical packaging
Plastic packaging for agrochemicals is prepared to carry those most aggressive substances. They are light and easy to handle, but solid and resistant enough to withstand contact with gases and chemical reactions without collapsing.
To be efficient, plastic packaging for agrochemicals must be able to contain the product, protect it, keep it and communicate to the consumer all important information.
As for containing the product, they must be resistant in order to transport the products from the place of production to their place of sale to the public without suffering from paneling.
In addition, plastic packaging for agrochemicals serves the function of protecting products from external agents such as light, gases, insects, moisture, etc., which could damage them. These containers must also be able to keep the product throughout the process so that it reaches the consumer while maintaining all its properties.
The last of the functions of these packaging is to communicate to the final consumer all the information relating to both the packaging and the content. They should contain information such as weight, the product it contains, emergency telephones, approval codes, etc.
To achieve all this, it is important that plastic packaging for agrochemicals is made with materials whose properties fulfill these functions without problems, and the choice of one type of plastic or another will depend mainly on the product and the conditions of the product.

Recycling of agrochemical packaging
Recycling plastic packaging for agrochemicals is a problem that has been of concern to the sector for years. But it is not the packaging itself that is the main actor in this concern, but rather its final use.
These containers, containing highly polluting substances, are not ordinary containers that can be recycled in the same mechanical way as many others.
In the case of plastic packaging for agrochemicals, the role of the end user is essential. He is bound to rinse the container several times with water, drill both the bottom and lid of the container to avoid reuse, and deposit it at specific points for collection.
As part of the commitment to the sustainability of packaging, there are programs to collect, recycle and prevent them from ending up in places where they can pollute land or water, so farmers' awareness of how dangerous their misuse is, is vital.
Plastic packaging for agrochemicals cannot be reused for other purposes, so it must be treated in a plant where they can be decontaminated, and the difficulty in controlling the end of each of them has made this one of the main problems in the sector.
Types of packaging for agrochemicals
At Alcion Packaging Solutions we have years of experience in the production of the agrochemical plastic packaging industry, and we know that choosing the right packaging is the key to avoiding the material, personal or economic damage these products can cause with the wrong packaging.
We sell bottles with capacities from 15 ml to 1 liter, and 5L and 10L jerrycans. We manufacture our packaging following the needs of each customer's product with technology such as multilayer coextrusion or plasma fluorination, getting containers with barrier properties, resistant and durable and, above all, environmentally friendly throughout the process.

According to United Nations statements, more than 6000 types of hazardous substances are currently circulating without adequate protection. This, consequently, could provoke serious material, personal and economic consequences. The way to prevent these substances from causing a problem is clear and simple: always pack your dangerous products with UN approved packaging.
What is “UN approval”?
In the process of producing and distributing hazardous substances, the manufacturer is responsible for using safe packaging. Any package containing these goods must meet minimum performance standards.
UN approval is the way to ensure that a packaging meets the conditions necessary to pack hazardous substances in a completely safe way. Besides, in some cases, hazardous substances can be distributed even without secondary packaging, as long as primary approved packaging is used, saving costs to the manufacturer.
When talking about approved packaging, it is the packaging manufacturer who has to comply with certain design and packaging standards. This plastic packaging will have to be tested and certified. A Test Laboratory will evaluate the physical and chemical performance to comply with the requirements of a quality management programme controlled by the Approval Authority.
An accredited testing Laboratory will check factors such as chemical compatibility with the product, the temperature that can withstand in good condition or physical resistance, among other characteristics of the packaging.
Once the Testing Laboratory informs the manufacturer of the positive results, it shall issue an approval act allowing the manufacturer to mark its approved packaging for the following 5 years, with that laboratory responsible for granting the extensions.
Having obtained the UN test report, the packaging producer will mark the UN code on each single package produced. This code will give the information on manufacturer's data, country, number and approval body, year of manufacture, packing group, test pressure and symbol of UN-verified packaging…
This information will ease the identification of an UN approved packaging and ensure traceability of packaging and compliance with all security measures established by the UN.
Packaging and regulations… requirements to be met?
All packaging of these hazardous goods is required to obtain this UN approval from an accredited official laboratory or by the competent authorities of the country of origin of the packaging manufacturer.
As mentioned above, one of the requirements for UN approval is to include in the packaging all the information relating to both the content and the packaging itself. Packaging must pass stacking and fall tests, among others, and must comply with the requirements imposed in relation to the substance it contains, quantity, weight, etc.
All these approved packaging requirements and regulations are set out in the ADR (European Agreement on the International Transport of Dangerous Goods). Annex A to this document includes all the actions that need to be taken in relation to packaging before sending a product and distributing it. This section includes actions to be carried out such as the classification of the goods, the generation of the relevant documentation, the pre-shipment controls of the goods, etc.
The ADR establishes 13 categories in order to classify dangerous goods, grouped according to their level of risk:
- GROUP I (X), Very Dangerous Materials.
- GROUP II (Y), Medium-hazardous materials.
- GROUP III (Z), Materials of minor hazard.
Annex B, on the other hand, includes all information relating to transport, the type of vehicle that will transport the goods, equipment, the choice of driver, etc.
These annexes are updated every two years, so all information regarding approved packaging iskept up to date and available on the internet.
However, the RID, IMDG, IATA and ICAO regulations also collect the necessary information for approved packaging for the maritime, air and rail transport of dangerous goods.
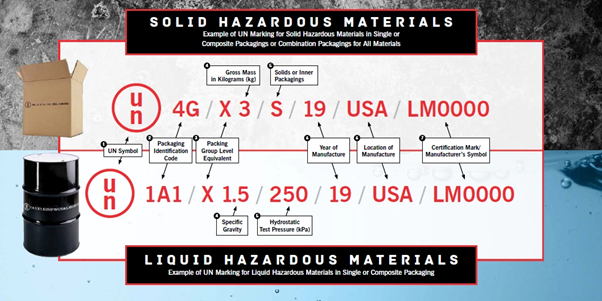
Infographic source: labelmaster.com
The packaging approved from the user's point of view
When manufacturing and putting dangerous substances into circulation, it is vitally important that it is carried out with safe packaging, as any personal or material damage they may cause would be the direct responsibility of the manufacturer.
However, it is also the consumer's responsibility to choose brands that meet all safety requirements and to do so, it is important to know how to identify them.
At the bottom of the packaging, the user can find the packing code. The first thing the user should check on approved packaging is that the code shows the symbol "UN" indicating that the regulations of the united nations are complied with. Knowing this, the user can have the guarantees that the packaging meets the specifications and requirements that the UN has imposed for the transport and sale of dangerous goods.
However, in addition, this code will continue with an arábiga figure, a composite code indicating for which substances such packaging is permitted and the degree of hazard, it will also indicate the relative density or maximum gross weight in kg, the year of manufacture, the country of approval, the number of registration in the official register and the name (or anagram) of the manufacturer.
This code must be permanently engraved in order to identify approved packaging throughout its useful life. Howver, approved packaging must also include a label where all this information remainsvisible. Non-compliance with UN packaging requirements or incomplete labelling could cause the sale or movement of the goods to be prohibited at the point of destination.
The dangerous goods packaging sector is complex, and any failure in packaging or sorting could incur large costs for the company that markets the product. Therefore, at Alcion Packaging Solutions, we believe that having the knowledge and control of approved packaging experts is essential to ensure that they are safe, comply with all current regulations and therefore cannot cause any personal injury or economic loss.
